Abrasive waterjet cutting
Waterjet high pressure pumps for abrasive cutting solutions by thyssenkrupp Industrial Solutions means the force of nature built into a single high pressure pump!
Just like the Colorado River was able to cut its way into the rocks and form the Grand Canyon, we help you to cut all sorts of materials. With our waterjet high pressure pumps this isn’t a process of many millions or thousands of years but happens almost as fast as the blink of an eye.
Imitating the nature and using water as a cutting method has been around for decades. But while early waterjets could perfectly handle soft materials, they were not able to cut harder materials such as metals in the same fashion. It took until the 1980s, when it showed that adding abrasives to the water stream could open new possibilities for cutting, which make it possible to cut harder materials as well without heat influence on the cutting edges.
Since then there are two common ways of waterjet cutting available: Pure water cutting and abrasive waterjet cutting.
Pure water cutting can be utilized to cut soft and hard materials – using abrasives and adding an abrasive cutting head gives waterjet cutting amazing capabilities to cut harder materials.
Depending on your specific requirements thyssenkrupp Industrial Solutions offers high pressure pumps for abrasive cutting in the range of 4000 bar and 6000 bar. In addition to high pressure pumps we offer a wide range of optional equipment like abrasive cutting heads and piping equipment.
Please contact us so we can offer you a tailormade solution for your operations!
Pure waterjet cutting vs. abrasive waterjet cutting
As its name implies, the pure waterjet works with water alone. A stream of highly pressurized water is directed onto the material-to-cut resulting in precise and clean slicing. This process might be enough for softer materials such as food or thin plastics but it is not powerful enough to cut harder materials. This is when the abrasive waterjet technology comes into play.
It does not differ in its operating principle from the pure waterjet cutting but makes use of abrasive particles, for example garnet. The abrasives are added to the stream of highly pressurized water pushed out of the machine’s nozzle. With the abrasives then hitting the target with high pressure and velocity it precisely erodes even the hardest materials such as steel and stone.
In contrast to the pure waterjet cutting, the water itself is no longer the tool for cutting – it’s the added abrasives that do the trick whereas the water stream just focusses them at the right spot.
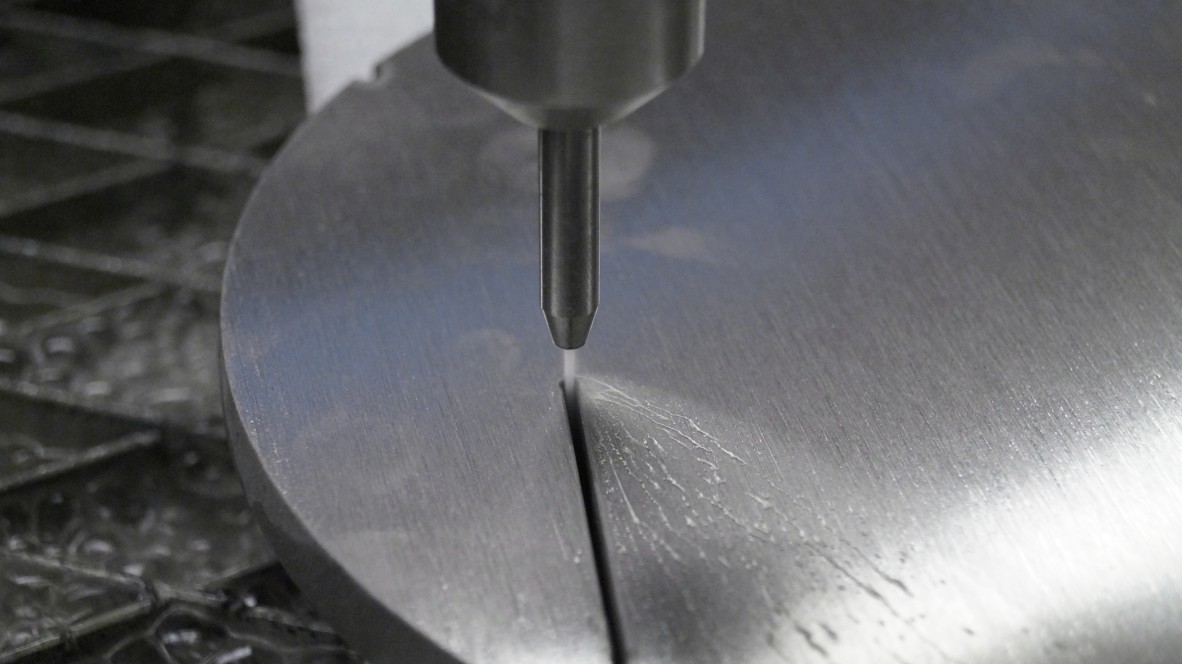
Abrasive Cutting
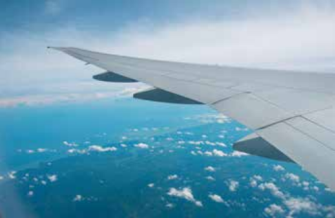
When to use abrasive waterjet cutting?
Abrasive water jet cutting is ideal for harder materials such as:
- Aluminium
- Steel & stainless steel
- Thick plastics
- Stone
- Ceramic
- Tiles
- Carbon
- Glass (standard glass, laminated glass, bulletproof glass, Plexiglas®)
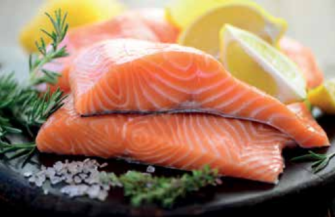
When to use pure waterjet cutting?
Pure waterjet cutting is ideal for softer materials such as:
- Food products (i.e. fish, meat, cake or vegetables)
- Leather
- Thin plastics
- Rubber
- Fabric
- Foam
- Wood-based materials, e.g. plywood
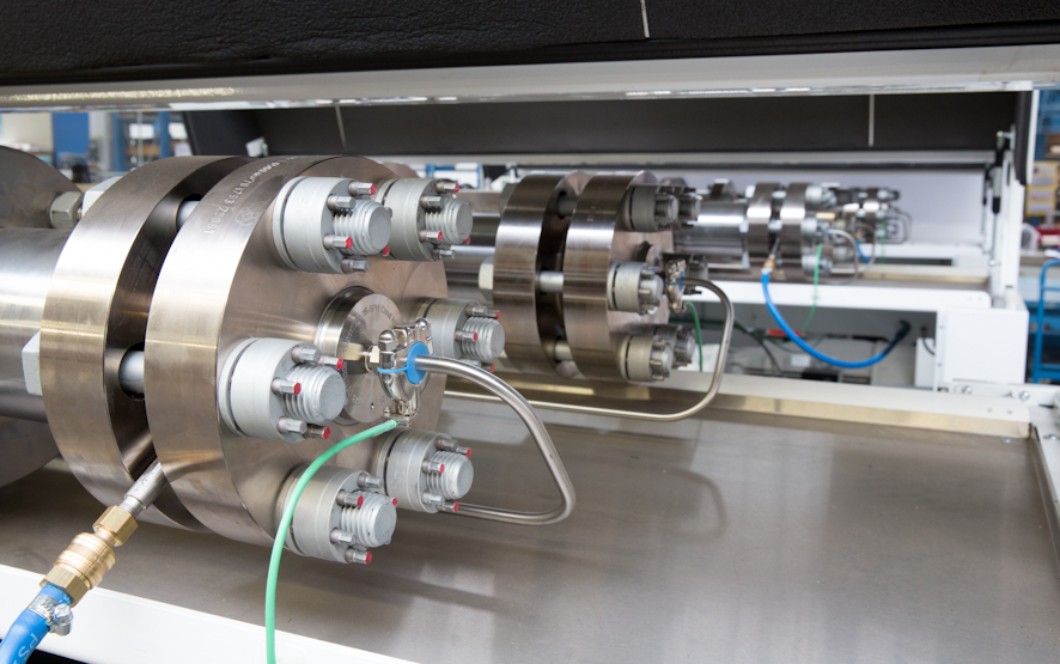
The advantages of abrasive waterjet cutting:
Abrasive waterjet cutting:
- can cut composite materials, e.g. coated metals, carbon and glass fiber compounds without any compromise or limitations
- is cost efficient on high-volume requirements because material can be processed in bundles
- generates little heat and produces clean and precise cuts
- applies extremely low mechanical load on the material, which avoids cracks or deformations
- can cut thermally sensitive materials without hardening or changing the physical properties
- can cut thicker materials at relatively high cutting speeds without burrs and the need for post-processing