Waterjet cutting
We experience the power of water daily. Water has been creating new shapes by erosion for millions of years. Uhde High Pressure Technologies applies this principle to waterjet cutting – with a significant difference: this time is simply reduced by increasing water pressure.
In competition with other processes such as laser and plasma cutting, waterjet cutting is increasingly developing into a real high performance process. Nowadays technology has advanced so much that multi-head and 5-axis systems are in operation, enabling cutting to be carried out on 3D components. Today pressures up to 4,000 bar are mainly used in waterjet or abrasive waterjet cutting technology.
A further considerable increase in performance and therefore enhanced productivity is only possible by raising the cutting pressure. In some cases economic efficiency can increase way above average when the cutting pressure is raised from 4000 bar to 6000 bar.
Regardless of the material composition and type, water cuts with maximum precision and flexibility. High pressure waterjet cutting is furthermore characterized by environmental and user friendliness. Due to its numerous advantages it is superior to other cutting processes and thus has evolved into one of the most important processes at all.
What does a waterjet cutting system bring to the cutting operation?
- almost any kind of material can be cut (steel, stainless steel, composites, glass, ceramics, stone, rubber etc.)
- no thermal effect on materials, low cutting and reaction forces, small cutting width (0.5-1.0mm)
- 2D and 3D applications
- max. cutting thickness up to 500 mm with 6,000 bar
- new application fields – e. g. miniaturization, surgery
At thyssenkrupp Industrial Solutions we offer specific solutions according to your waterjet cutting requirements. If you require a pure water solution or an abrasive cutting solution by using an abrasive cutting head, we provide high pressure pumps starting from 4000 bar. For both applications we offer the 6000 bar high pressure pump.
Water jet cutting applications
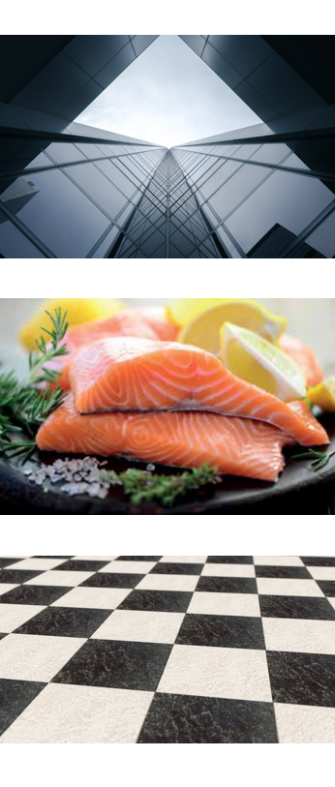
Industries that benefit significantly from the use of water jet cutting:
- Aerospace
- Agriculture
- Automotive
- Building industry
- Energy
- Food industry
- Job Shops
- Laboratory Equipment
- Marine
- Medical
- Military
- Oil & Gas
- Semiconductor
- Transportation
Various applications for abrasive and pure water jet cutting
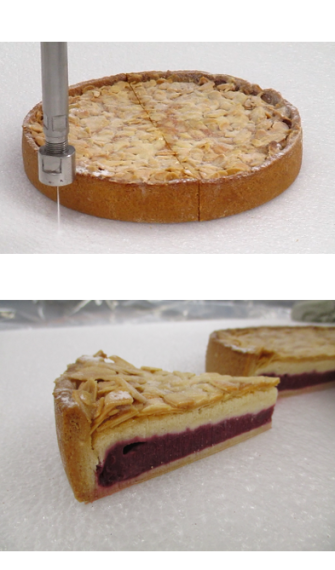
Water jet cutting for the food industry
Pure water jet cutting is the state-of-the-art manufacturing process to cut a wide range of foods. Meats, fish, poultry, frozen foods, cakes and even candy bars or pizza are cut with the power of pure water.
Of course, this would not be the case if the method did not offer any advantages over other cutting processes.
Using water jet technology to cut food:
- Ensures a sanitary environment. Because no blades or metal cutting is necessary, there isn’t any cross contamination from tool to food or food to food.
- Uses neither chemicals nor heat
- Enables higher productivity. Because no blades are used, there is no need for changing or sharpening any blades. Therefore, no downtimes occur. In addition, the small kerf provides for almost no waste and makes sure that the food won’t be compressed or washed out resulting in longer shelf life.
- Ensures extremely high cut quality allowing for a clean edge without smearing or tearing
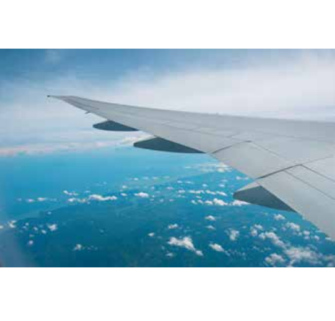
Water jet cutting for the aerospace industry
Abrasive water jet cutting is perfectly suited for the aerospace industry since it is able to cut aluminum, steel, titanium, brass and various composites all alike. This allows for precise cutting of airplane fuselages, rotary blades and wing and tail sections for example.
Advantages using abrasive water jet cutting for aerospace are:
- No burrs and rough edges occur
- No Heat-Affected Zones
- Less material waste
- Increased productivity because of faster cutting
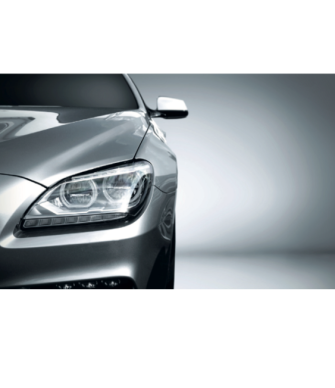
Water jet cutting for the automotive industry
Water jet cutting whether pure or abrasive is a perfect solution for automotive. Because of its versatility, it is able to cut materials such as aluminum, steel and composites as well as door panels or carpet for the car interior.
Advantages using water jet technology to cut in automotive are:
- No burrs and rough edges occur
- No Heat-Affected Zones and noxious fumes
- Less material waste
- No mechanical stresses on the surface of the cuts
- Increased productivity because of faster cutting
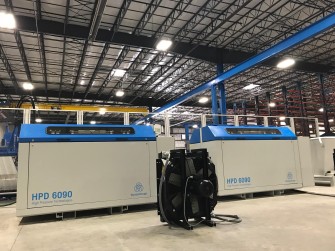
Water jet cutting for the medical industry
When it comes to the manufacturing of life-saving medical implants and instruments as well as surgical instruments there is nothing more important than precision and to meet the highest quality standards. Abrasive water jet cutting is able to guarantee both since it cuts with the highest accuracy and precisely shapes materials without undesirable side effects.
Advantages using abrasive water jet cutting for medical implants and instruments are:
- No Heat-Affected Zones and therefore no surface hardening and changes their intrinsic properties
- No toxic and hazardous waste materials
- Minimal kerf allows for high precision cuts
- Cut angles that common machines can’t cut
- Less material waste
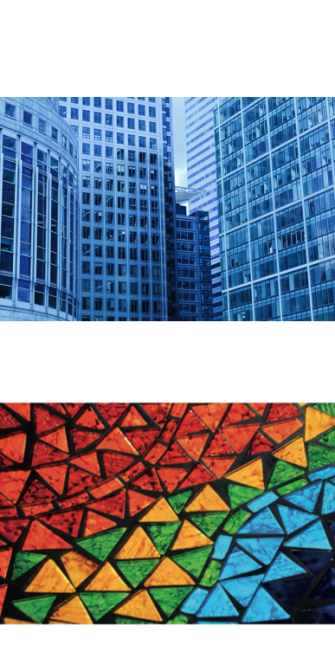
Water jet cutting for glass
Abrasive water jet cutting is able to handle different kinds of glasses such as standard glass, laminated glass, bulletproof glass and Plexiglas®. This opens up a multitude of applications that can be cut with the power of the water jet and the addition of an abrasive. This includes:
- Lenses
- Mirrors
- Optical laser parts
- Glass items for the electronic & medical industry
- Window panels
- Glass ornaments & church mosaics
- Inlays for tabletops
- Light fixtures
Advantages using water jet technology for glass cutting are:
- No rough edges occur
- Cut angles that common machines can’t cut
- No Heat-Affected Zones
- Less material waste
- Minimal kerf allows for incredible detailed cuts
- Increased productivity because of faster cutting
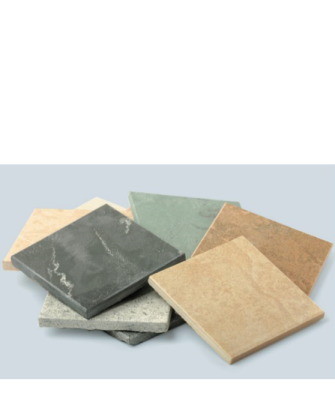
Water jet cutting for stone and tile
With abrasive water jet cutting you are able to cut all sorts of stones and tiles such as granite, limestone, slate and marble among other materials for floors as well as ceramic tiles or sinkholes for kitchens or bathrooms.
Advantages using abrasive water jet cutting for stones and tiles are:
- No rough edges occur
- Compared with cutting with blades and saws no toxic dust or waste occurs
- Less material waste
- The minimal kerf allows for artistic and detailed patterns
- Increased productivity because of faster cutting and no need for changing or sharpening any blades
- No risk of deformation and discolouring